Reduction of foaming
We are able to prepare and manage any type of carbonated beverage present on the market, both clear and with pulps or fibres, with an extensive range of carbonation levels (from 2 vol. to 4.5 vol. of CO2).
It is very important to optimise the manufacturing process of a CSD bottle (preform project – process) to reach physical-mechanical characteristics required by the product. PET is one of the preferred packaging materials, it is transparent, light, unbreakable and can easily be customised into a wide variety of shapes. It offers a good barrier to gas, namely to carbon dioxide.
The two major requirements of a container for carbonated soft drinks are its capacity to maintain the CO2 content inside the product for as long as possible, and to resist bottle expansion due to internal pressure. It is therefore very important to optimise the manufacturing process of a CSD bottle (preform project – process) to reach physical-mechanical characteristics required by the product.
- Preserve CO2 levels inside the packaging. This is important especially for small size containers.
- Reduced bottle expansion due to internal pressure (Shape keeping).
- Containers must pass burst and drop tests.
- Shape and bottom designed to resist high internal pressure (creep and burst resistance).
- Reduce bottle weight while assuring bottle stability
01
High mechanical performance
02
Base optimised for resistance to stress cracking
03
Good resistance to internal pressure
04
CO2 barrier
MATERIAL:
- PET, recycled and reground PET, Barrier PET, bio-based materials like PEF
BARRIER CONTAINERS:
- in order to prolong the product's shelf life, containers can be produced with different types of barriers. The bottles production can be made with the addition of barrier agents blended with the resin (nylon MXD6, EVOH, oxygen scavengers), with the production of multilayer containers (PET+EVOH or PET + Nylon)
SHAPES:
- round, customised, contour, swirl, Global Swirl
SIZES:
- from 250 ml to 5 litres
WEIGHT:
- ffrom 10 grams for 100 ml to 120 grams for 5 litres, lightweight containers design
NECK DIAMETER:
- from 26 mm to 38 mm
- Our Machinery / 01
- SIPA
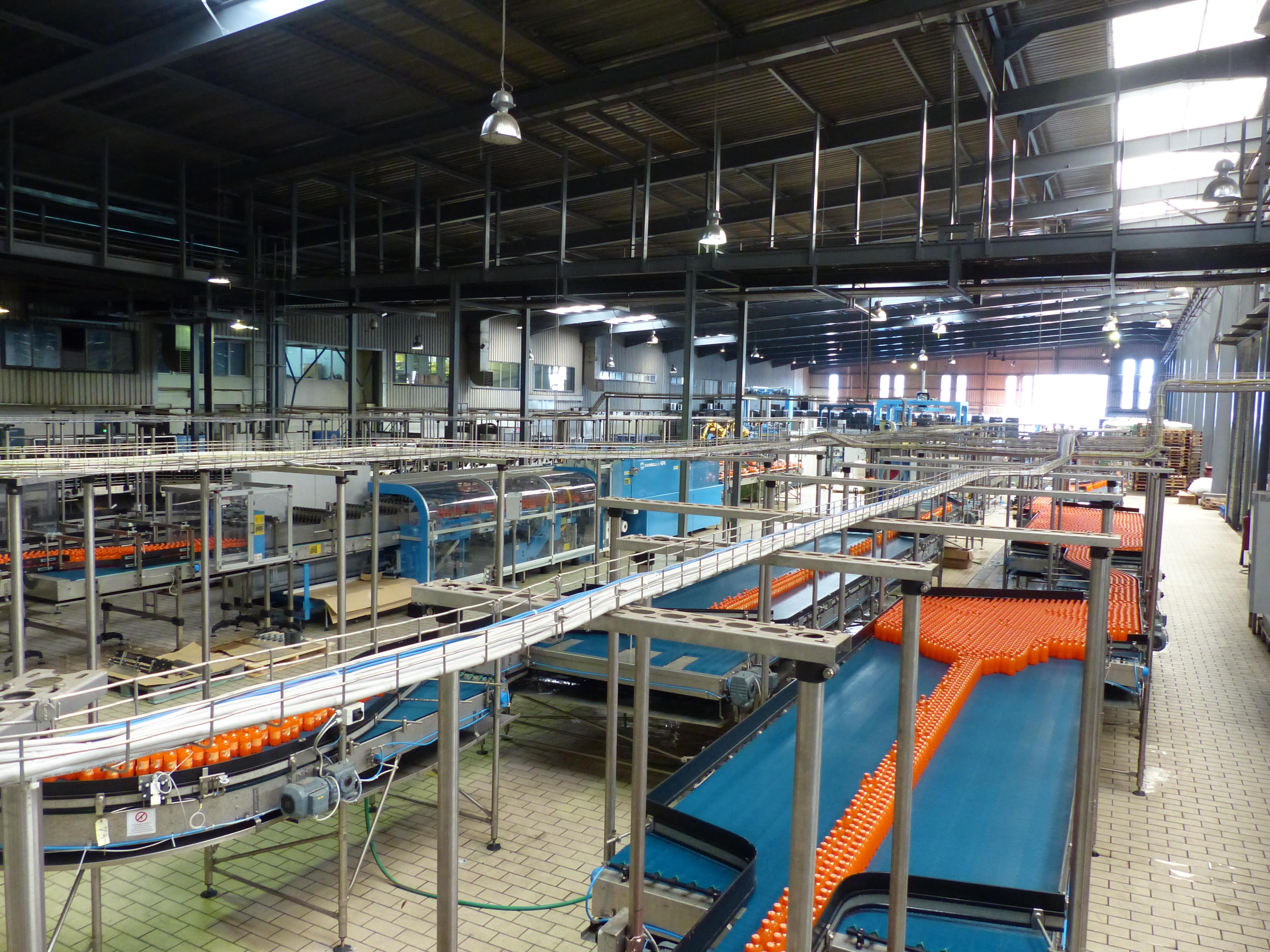