MODEL | CAPACITY |
Xblend 12 | Up to 12,000 l/h |
Xblend 27 | Up to 27,000 l/h |
Xblend 34 | Up to 34,000 l/h |
Xblend 42 | Up to 42,000 l/h |
Xblend 54 | Up to 54,000 l/h |
Xblend 66 | Up to 66,000 l/h |
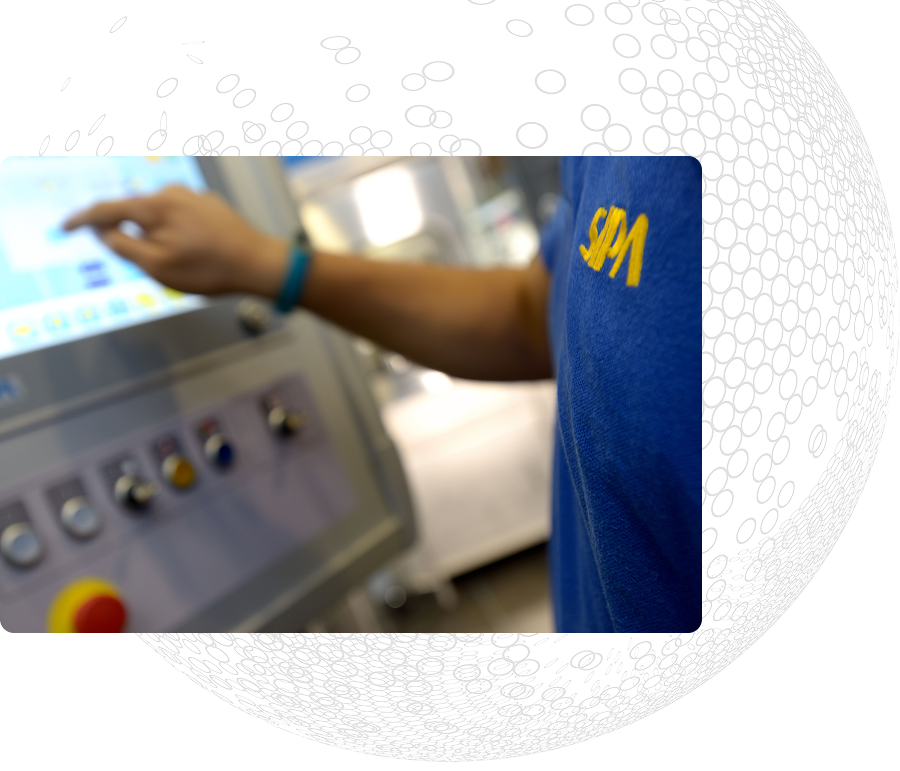
Degassing
The inlet water is deaerated inside a tank by using nozzles, in high vacuum atmosphere (excludable). A magnetic flow meter counts the water that is sent to the mixing system by using a centrifugal pump.
Blending
The inlet syrup is monitored by using a mass flow meter to adjust, if necessary, the dilution ratio in order to maintain and to ensure the maximum accuracy and the maximum repeatability of the final beverage.
A special diffuser is installed to obtain an homogeneous dissolution of the desired syrup quantity, moreover the dispersion of gas is realized through a further static mixer that ensures a fine mixing of the finished beverage.
MODEL | CAPACITY |
Xblend 12 | Up to 12,000 l/h |
Xblend 27 | Up to 27,000 l/h |
Xblend 34 | Up to 34,000 l/h |
Xblend 42 | Up to 42,000 l/h |
Xblend 54 | Up to 54,000 l/h |
Xblend 66 | Up to 66,000 l/h |
Artificial Intelligence is reshaping the packaging world, unlocking rapid concept generation and previously unthinkable creative possibilities. But while AI can create countless virtual container...
SIPA is pleased to announce the successful implementation of its enhanced Remote Technical Support Service, now operating 24 hours a day, 7 days a week, since its launch in March 2025. This...
Meeting Industry DemandsIn today's dynamic packaging landscape, manufacturers demand agility and efficiency in their production processes. Recognizing this need
In the packaging market, SIPA is one of the few companies offering a complete range of solutions for large containers up to 5 gallons such as design, engineer
With an overall score of 78/100 (97th percentile) SIPA has been awarded a Gold medal from EcoVadis Sustainability Rating for the year 2025 placing us among th
Artificial Intelligence is reshaping the packaging world, unlocking rapid concept generation and previously unthinkable creative possibilities. But while AI can create countless virtual container...
SIPA is pleased to announce the successful implementation of its enhanced Remote Technical Support Service, now operating 24 hours a day, 7 days a week, since its launch in March 2025. This...
Meeting Industry DemandsIn today's dynamic packaging landscape, manufacturers demand agility and efficiency in their production processes. Recognizing this need
In the packaging market, SIPA is one of the few companies offering a complete range of solutions for large containers up to 5 gallons such as design, engineer
With an overall score of 78/100 (97th percentile) SIPA has been awarded a Gold medal from EcoVadis Sustainability Rating for the year 2025 placing us among th
SIPA Packaging Development team has secured a significant project with Family Group, a prominent beverage company hailing from Uzbekistan and the owner of
SIPA Packaging Development team has secured a significant project with Family Group, a prominent beverage company hailing from Uzbekistan and the owner of
The first Sipa 200-cavity preform mould in Asia is now in operation at Sappe, a major Thai beverage producer, further cementing SIPA's leadership in innovative preform manufacturing solutions.
SIPA is pleased to announce a major collaboration with Gepp, the Mexican bottler of Pepsi products, empowering them to significantly reduce their environmental footprint while achieving substantial...
SIPA is pleased to announce a major collaboration with Gepp, the Mexican bottler of Pepsi products, empowering them to significantly reduce their environmental footprint while achieving substantial...
SIPA Packaging Development team has secured a significant project with Family Group, a prominent beverage company hailing from Uzbekistan and the owner of
SIPA Packaging Development team has secured a significant project with Family Group, a prominent beverage company hailing from Uzbekistan and the owner of
The first Sipa 200-cavity preform mould in Asia is now in operation at Sappe, a major Thai beverage producer, further cementing SIPA's leadership in innovative preform manufacturing solutions.
SIPA is pleased to announce a major collaboration with Gepp, the Mexican bottler of Pepsi products, empowering them to significantly reduce their environmental footprint while achieving substantial...
SIPA is pleased to announce a major collaboration with Gepp, the Mexican bottler of Pepsi products, empowering them to significantly reduce their environmental footprint while achieving substantial...
Please let us know how we can assist you. We have dedicated contact forms for specific inquiries, ensuring your request reaches the right department for a swift and accurate response.
Drinktec | 2025