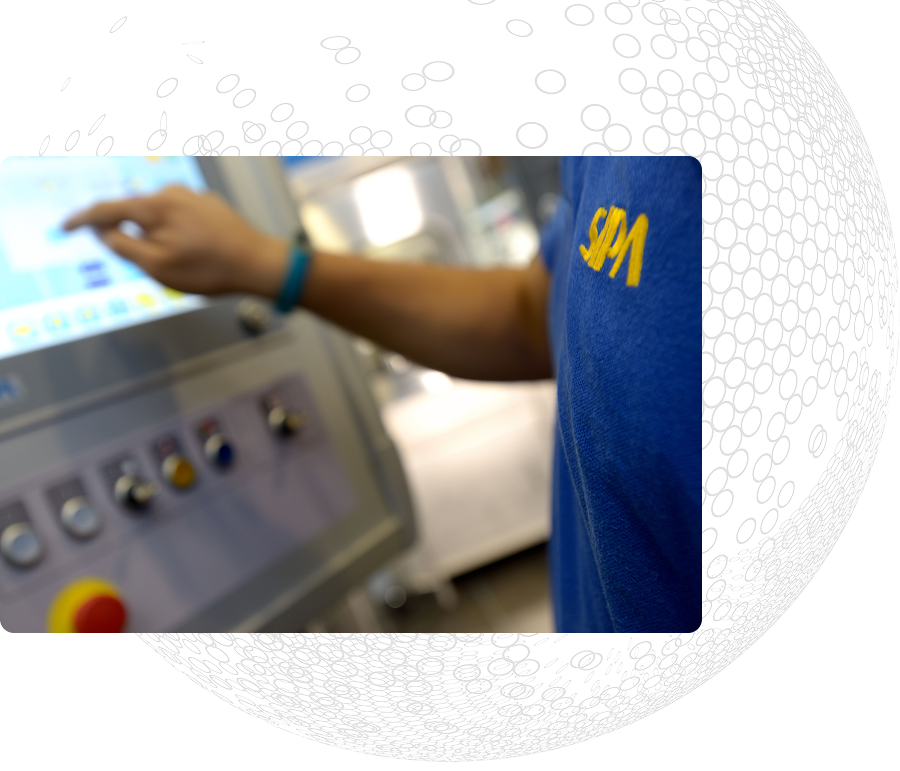
XMOULD is an innovation from Sipa which allows reduction of friction between molten PET and molding surface of the injection stacks during injection phase, allowing production of thin-wall performs with length on wall thickness ratio above 50 (L/t in the range of 50 to 55 possible), so better/optimized thickness distribution on final packaging (avoid the accumulation of material on zone as under-neck and bottom areas).
XMOULD technology givesdesigners the power to create lightweighted preforms which do not compromise performance of the final container.Besides the possibility to reduce preform thicknesses, this solution also improves cycle times due to friction reduction at filling phase.
Available on new or legacy tooling, only special injection stacks are required to enjoy the XMOULD technology, no changes required neither on the machine nor the hot runner.
Range of solutions on shaping components to extend the life of the cold half of our preform molds (optional).
11million life cycles guaranteed (flash < 0.2mm) without need of components refurbishing, following lifetime conditions. Significantly reduced refurbishment costs.
Our range of solutions is wide and versatile. We can supply moulds with up to 200 cavities for standard applications like mineral water or soft drinks, however we have a wide range of solutions also for special applications like wide mouth preforms or long preforms for 5 gallon containers.
Our flexible conversion and refurbishment services help you make the most of your tooling. For example, our LongLife service extends the life of preform mould cold halves up to 12 million cycles before first maintenance is needed.
SIPA supplies blow moulds for the beverage, food, and consumer goods industry to fit most of the major brands of re-heat stretch blow moulder machines. Our blowing specialists can advise you on how to achieve the best possible bottle quality even before the start of the production.In our laboratories, extensive tests and inspections are performed on both molds and sample bottles through high-quality measuring and testing equipment. SIPA produces aluminum and stainless steel moulds for any...
In second place in the world for the production of molds, SIPA is able to deliver global tooling programs for new molds or mold conversions from single to 200 cavities. To ensure top quality, every SIPA mold is tested before shipping on dedicated XFORM machines.
Artificial Intelligence is reshaping the packaging world, unlocking rapid concept generation and previously unthinkable creative possibilities. But while AI can create countless virtual container...
SIPA is pleased to announce the successful implementation of its enhanced Remote Technical Support Service, now operating 24 hours a day, 7 days a week, since its launch in March 2025. This...
Meeting Industry DemandsIn today's dynamic packaging landscape, manufacturers demand agility and efficiency in their production processes. Recognizing this need
In the packaging market, SIPA is one of the few companies offering a complete range of solutions for large containers up to 5 gallons such as design, engineer
With an overall score of 78/100 (97th percentile) SIPA has been awarded a Gold medal from EcoVadis Sustainability Rating for the year 2025 placing us among th
Artificial Intelligence is reshaping the packaging world, unlocking rapid concept generation and previously unthinkable creative possibilities. But while AI can create countless virtual container...
SIPA is pleased to announce the successful implementation of its enhanced Remote Technical Support Service, now operating 24 hours a day, 7 days a week, since its launch in March 2025. This...
Meeting Industry DemandsIn today's dynamic packaging landscape, manufacturers demand agility and efficiency in their production processes. Recognizing this need
In the packaging market, SIPA is one of the few companies offering a complete range of solutions for large containers up to 5 gallons such as design, engineer
With an overall score of 78/100 (97th percentile) SIPA has been awarded a Gold medal from EcoVadis Sustainability Rating for the year 2025 placing us among th
SIPA Packaging Development team has secured a significant project with Family Group, a prominent beverage company hailing from Uzbekistan and the owner of
SIPA Packaging Development team has secured a significant project with Family Group, a prominent beverage company hailing from Uzbekistan and the owner of
The first Sipa 200-cavity preform mould in Asia is now in operation at Sappe, a major Thai beverage producer, further cementing SIPA's leadership in innovative preform manufacturing solutions.
SIPA is pleased to announce a major collaboration with Gepp, the Mexican bottler of Pepsi products, empowering them to significantly reduce their environmental footprint while achieving substantial...
SIPA is pleased to announce a major collaboration with Gepp, the Mexican bottler of Pepsi products, empowering them to significantly reduce their environmental footprint while achieving substantial...
SIPA Packaging Development team has secured a significant project with Family Group, a prominent beverage company hailing from Uzbekistan and the owner of
SIPA Packaging Development team has secured a significant project with Family Group, a prominent beverage company hailing from Uzbekistan and the owner of
The first Sipa 200-cavity preform mould in Asia is now in operation at Sappe, a major Thai beverage producer, further cementing SIPA's leadership in innovative preform manufacturing solutions.
SIPA is pleased to announce a major collaboration with Gepp, the Mexican bottler of Pepsi products, empowering them to significantly reduce their environmental footprint while achieving substantial...
SIPA is pleased to announce a major collaboration with Gepp, the Mexican bottler of Pepsi products, empowering them to significantly reduce their environmental footprint while achieving substantial...
Please let us know how we can assist you. We have dedicated contact forms for specific inquiries, ensuring your request reaches the right department for a swift and accurate response.
Drinktec | 2025